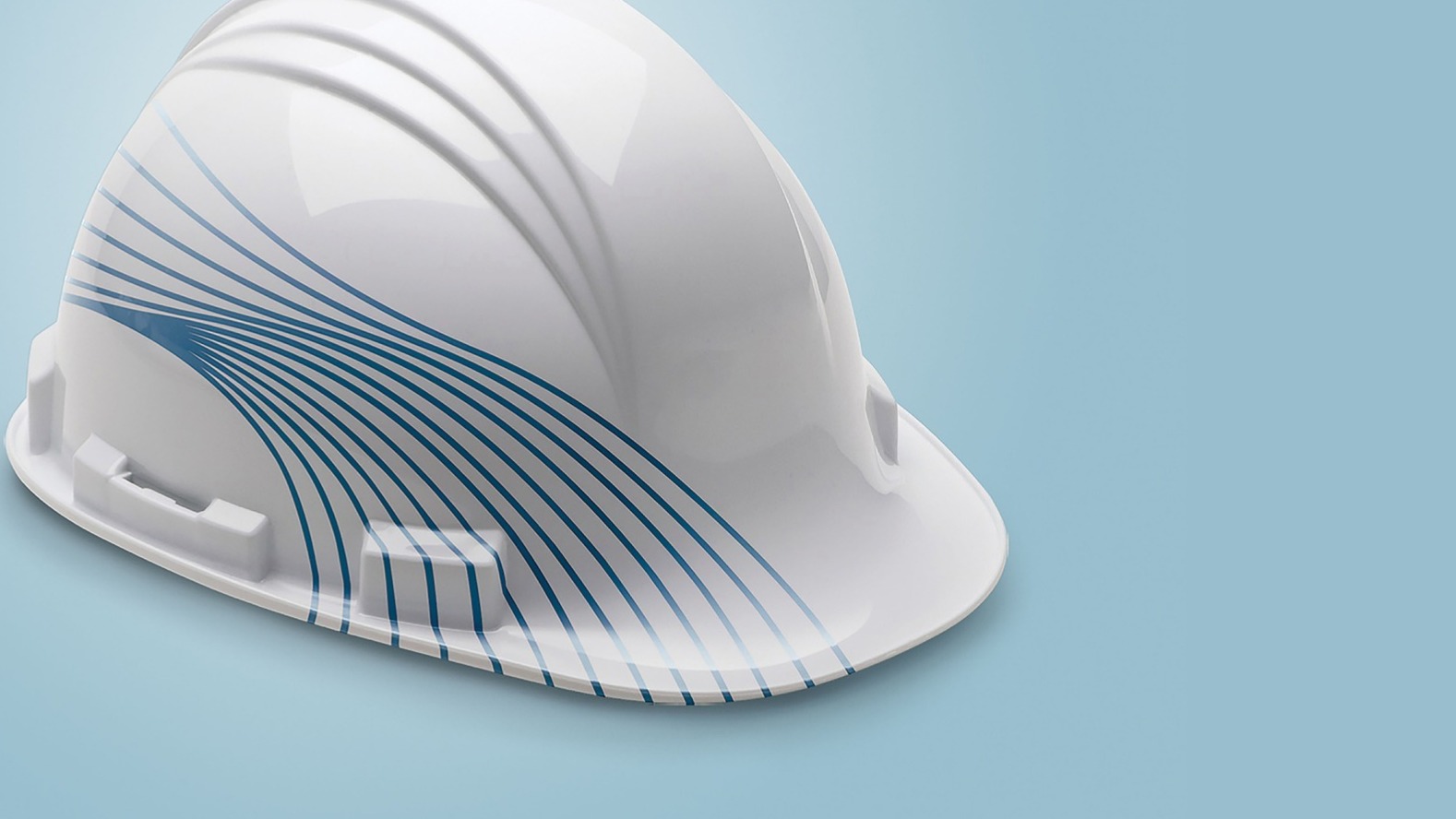
Application Temperature Limits in Insulation
Insulation Materials Temperature Limits and its Application
Table of Contents
- Introduction
- Understanding Insulation Materials
- Application Temperature Limits
- Temperature Limits for Every Insulation Material
- Factors Influencing Temperature Limits
- Selection of Insulation Materials
- Testing and Certification
- Best Practices for Application
- Case Studies and Examples
- Future Developments and Innovations
- Conclusion
Introduction
Insulation materials play a vital role in various industries, providing thermal protection and energy efficiency. However, it's crucial to understand the application temperature limits of these materials to ensure their optimal performance and longevity. In this article, we will delve into the significance of temperature limits in insulation materials and processes, exploring the factors influencing these limits and the best practices for their application.
Insulation materials are designed to withstand specific temperature ranges, and exceeding these limits can have adverse effects on their performance. Therefore, it's essential to select the appropriate insulation material that matches the intended application's temperature requirements. Let's explore the key aspects related to application temperature limits in insulation materials.
Understanding Insulation Materials
Before diving into temperature limits, it's essential to have a basic understanding of the different types of insulation materials available. These can include fiberglass, foam, mineral wool, cellulose, and reflective insulation, among others. Each material has unique properties that determine its suitability for specific temperature ranges and applications.
Application Temperature Limits
Application temperature limits refer to the range within which an insulation material can effectively function without compromising its performance. These limits vary depending on the material's composition, structure, and thermal properties. Exceeding the specified temperature limits can lead to reduced insulation efficiency, decreased durability, and potential failure of the insulation system.
Understanding the consequences of surpassing temperature limits is crucial. High temperatures can cause insulation materials to degrade, lose their insulating properties, or even release harmful substances. Conversely, extremely low temperatures can make some materials brittle and prone to cracking, compromising their effectiveness.
Temperature Limits for Every Insulation Material
Matching temperature limits with application requirements is crucial when selecting insulation materials. Different applications have specific temperature demands, and it's important to choose insulation materials that can withstand the required temperature ranges.
Fiberglass Insulation:
- Temperature Limit: Typically suitable for temperatures ranging from -40°C (-40°F) to 232°C (450°F).
- Higher temperature variants may withstand temperatures up to 538°C (1000°F) for short durations.
- Ideal for residential and commercial buildings, HVAC systems, and industrial applications with moderate temperature variations.
Mineral Wool Insulation:
- Temperature Limit: Generally suitable for temperatures ranging from -40°C (-40°F) to 815°C (1500°F).
- Higher temperature variants may withstand temperatures up to 1093°C (2000°F) for short durations.
- Well-suited for industrial processes, high-temperature equipment, furnaces, and fire-resistant applications.
Cellulose Insulation:
- Temperature Limit: Typically suitable for temperatures ranging from -40°C (-40°F) to 93°C (200°F).
- Higher temperature variants may withstand temperatures up to 135°C (275°F) for short durations.
- Commonly used in residential and commercial buildings, attics, and walls where moderate temperature insulation is required.
Spray Foam Insulation:
- Temperature Limit: Generally suitable for temperatures ranging from -40°C (-40°F) to 82°C (180°F).
- Higher temperature variants may withstand temperatures up to 121°C (250°F) for short durations.
- Ideal for sealing gaps, attics, walls, and areas requiring airtight insulation and moderate temperature resistance.
Polyurethane Foam Insulation:
- Temperature Limit: Typically suitable for temperatures ranging from -40°C (-40°F) to 82°C (180°F).
- Higher temperature variants may withstand temperatures up to 121°C (250°F) for short durations.
- Often used in buildings, refrigeration units, and areas requiring high insulation performance and moderate temperature resistance.
Expanded Polystyrene (EPS) Insulation:
- Temperature Limit: Generally suitable for temperatures ranging from -40°C (-40°F) to 74°C (165°F).
- Higher temperature variants may withstand temperatures up to 93°C (200°F) for short durations.
- Commonly used in construction, cold storage, and areas with moderate temperature variations.
Extruded Polystyrene (XPS) Insulation:
- Temperature Limit: Typically suitable for temperatures ranging from -40°C (-40°F) to 75°C (167°F).
- Higher temperature variants may withstand temperatures up to 93°C (200°F) for short durations.
- Frequently used in foundations, roofs, and areas where moisture resistance and moderate temperature insulation are needed.
Factors Influencing Temperature Limits
Several factors influence the temperature limits of insulation materials. The material's composition and structure, including its chemical makeup, density, and arrangement of fibers or particles, play a significant role. Thermal conductivity and resistance also affect how well the material can handle temperature fluctuations.
Environmental factors should also be considered. Humidity, exposure to ultraviolet (UV) radiation, and chemical interactions can impact insulation performance. Some materials may require additional protective coatings or barriers to maintain their temperature resistance in challenging environments.
Selection of Insulation Materials
Choosing the right insulation material involves matching its temperature limits with the specific application requirements. Different industries have distinct temperature demands, such as construction, automotive, aerospace, and industrial processes. It's crucial to consult industry guidelines and experts to ensure the selected insulation material can withstand the intended temperature conditions.
Testing and Certification
To verify the temperature limits of insulation materials, rigorous testing procedures are conducted according to industry standards. Certifications, such as the ASTM International standards, provide reassurance of compliance with quality and safety requirements. Before selecting an insulation material, it's essential to review its testing and certification documentation.
Here are some prominent industry standards and certifications for testing insulation materials:
ASTM International:
- ASTM C167 - Standard Test Procedures for the Density and Thickness of Thermal Insulating Blankets or Batts.
- ASTM C518 - Standard Test Method for Steady-State Thermal Transmission Properties by Means of the Heat Flow Meter Apparatus
- ASTM C687 - Standard Practice for Determination of Thermal Resistance of Loose-Fill Building Insulation
- ASTM C1338 - Standard Test Method for Determining Fungi Resistance of Insulation Materials and Facings
UL (Underwriters Laboratories) Certifications:
- UL 723 - Standard for Test for Surface Burning Characteristics of Building Materials
- UL 94 - Standard for Tests for Flammability of Plastic Materials for Parts in Devices and Appliances
- UL 181 - Standard for Factory-Made Air Ducts and Air Connectors
- UL 790 - Standard Test Methods for Fire Tests of Roof Coverings
ISO (International Organization for Standardization):
- ISO 6946 - Building components and building elements - Thermal resistance and thermal transmittance - Calculation method
- ISO 8302 - Thermal insulation - Determination of steady-state thermal resistance and related properties - Guarded hot plate apparatus
EN (European Norm) Standards:
- EN 12667 - Thermal performance of building materials and products - Determination of thermal resistance by means of guarded hot plate and heat flow meter methods - Products of high and medium thermal resistance
- EN 13501 - Fire classification of construction products and building elements
These standards and certifications ensure that insulation materials are tested for various properties such as thermal resistance, fire resistance, density, flammability, and resistance to fungi or other environmental factors. Compliance with these standards and certifications provides confidence in the performance, durability, and safety of the insulation materials.
It's important to note that specific standards and certifications may vary depending on the region or country. When selecting insulation materials, it is recommended to check for compliance with relevant standards and certifications specific to your location and intended application.
Best Practices for Application
Proper application techniques and installation practices are vital to maximize insulation performance and adhere to temperature limits. Pre-installation considerations, such as surface preparation, moisture management, and compatibility with other building components, should be addressed. During installation, following manufacturer guidelines and utilizing recommended tools and accessories ensures optimal results.
Maintaining and monitoring insulation systems over time is equally important. Regular inspections, addressing any damage or deterioration promptly, and implementing maintenance routines can help prolong the effectiveness of insulation materials within their temperature limits.
Case Studies and Examples
Real-world examples provide valuable insights into the consequences of neglecting temperature limits in insulation applications. Highlighting case studies of insulation failures due to temperature issues, such as thermal runaway in electrical components or heat transfer in industrial processes, reinforces the importance of considering temperature limits.
Future Developments and Innovations
The field of insulation materials continues to evolve, with ongoing research and innovations focused on enhancing temperature resistance. Advances in nanotechnology, aerogels, and phase-change materials show promising potential for future insulation solutions capable of withstanding extreme temperature conditions.
Conclusion
In conclusion, understanding and respecting the application temperature limits of insulation materials are essential for ensuring their optimal performance and longevity. By selecting the appropriate material, considering factors such as composition, thermal properties, and environmental conditions, the risk of insulation failure due to temperature-related issues can be minimized.
Adhering to industry standards, best practices, and continuous monitoring of insulation systems contribute to the overall efficiency and effectiveness of insulation in various applications. Call Wichita Insulation Pros to learn more about insulation.